MR485E Synchro Trainer Electrical Training Equipment Vocational Training Equipment
1. Equipment introduction
1.1 Overview
The synchronous trainer is mainly composed of a power module, an auto-angle machine module (auto-angle transmitter + auto-angle receiver + auto-angle transformer), a voltage module and a current module.
The self-aligning machine module (self-aligning transmitter + self-aligning receiver + self-aligning transformer) is a multifunctional independent demonstration system that can be used to study and demonstrate the principles and working principles of AC synchronous transmitters and receivers, and to master Its control principles and control methods cultivate students' corresponding knowledge and skills.
1.2 Features
(1) Two or both are required to be used at the same time.
(2) When two or two are used at the same time, there is no mechanical connection with each other, only electrical connection.
(3) The non-contact self-aligning machine is safe and reliable in operation, has a long life, and is more reliable in environments lacking maintenance and in any system subject to bumps and vibrations.
(4) The training platform is made of aluminum industrial column profiles to ensure the stability of the training platform; the bottom universal wheels are equipped with brakes and can be flexibly moved and positioned. The training platform is safe to operate (multiple personal and equipment safety protections), standardized, flexible, solid, durable, beautiful and modern.
(5) The experimental circuits and devices are fully configured and can be used in combination to complete practical training content for a variety of subjects.
(6) The training platform has a good safety protection system.
2. Technical parameters
Input power: One-way 230V±10%, 50Hz
weight: 78KG
size : 1240x720x1290mm
The altitude does not exceed 1000m
Ambient temperature -40℃~+55℃ (humidity is 60%-70%)
Relative humidity 95%±3% (air temperature is 20±5%)
3. Components list and detailed introduction
3.1 Main part
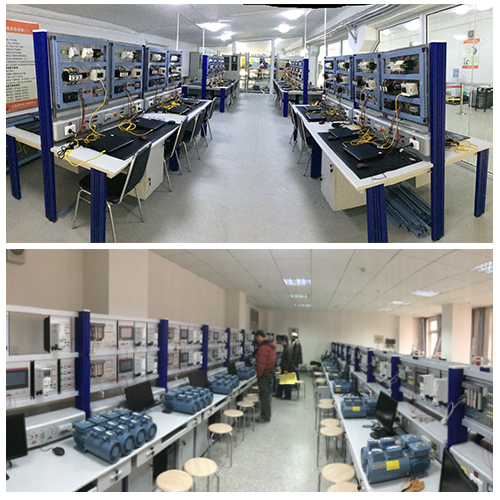
No Name
1 main frame
2 console
3 Experimental module
4 Universal wheel
3.2 Experimental module part
No Name
1 breaker
2 Step-down isolation transformer
3 Synchronous transmitter (self-aligning machine transmitter)
4 Transmit signal module
5 AC digital voltmeter
6 AC analog ammeter
7 AC analog voltmeter
8 Rocker switch SW1
9 Rocker switch SW2
10 Power rocker switch
11 Connection terminal
12 Rotary Switches
3.3 Equipment configuration list
No Name Qty
Component 1 Training table 1
Component 2 Universal wheel 4
Component 3 breaker 1
Component 4 Step-down isolation transformer 1
Component 5 rocker switch 3
Component 6 AC analog voltmeter 1
Component 7 AC digital voltmeter 1
Component 8 AC analog ammeter 1
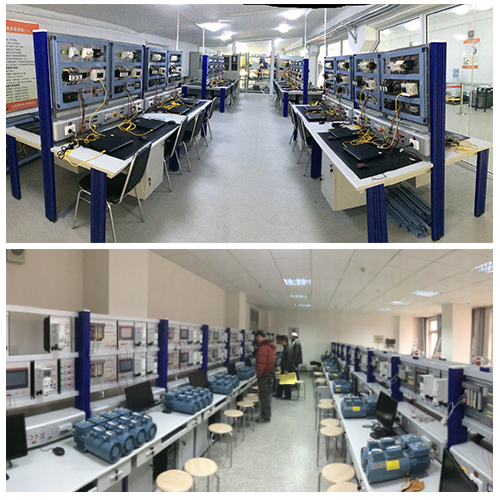
Component 9 Synchronous transmitter module (self-aligning machine transmitter) 1
Component 10 Synchronous receiver module (self-aligning machine receiver) 1
Component 11 Rotary Switches 2
Component 12 Connection terminal 29
3.4 Accessories
No Name Qty
1 K4 safety connection cable(yellow) 10
2 K4 safety connection cable(red) 10
3 K4 safety connection cable(blue) 10
4 K4 safety connection cable(green) 10
5 K4 safety connection cable(double) 10
6 fuse(2A) 5
7 fuse(5A) 5
4. Experiment list
Experiment 1 Introduction to self-aligning machine
Experiment 2 Analysis of Synchronous Transmission System
Experiment 3 Voltage measurement of synchronous transmitter and synchronous receiver at different time points
Experiment 4 Analysis of the similarities between synchronized transmitters and receivers and phase pairing
Experiment 5 Analysis of the differences between synchronized transmitters and receivers and phase pairing
Experiment 6 Current of different loads in the circuit
Experiment 7 Controlling motor speed and analysis of forward and reverse directions
Experiment 8 Control Principle of Closed-Loop Control System