MR106A Electric Vehicle Vacuum Assisted Hydraulic Brake System Training Equipment Automotive Trainer Technical Training Equipment
I.System composition
This test bench uses an electric vehicle ABS system, and the original vehicle has an improved structure bench layout.
The display panel uses an aluminum-plastic panel. The control panel is painted with an intuitive electronic control system schematic diagram consistent with the original vehicle control system. It has a personalized operating platform, working condition indicator lights, motor switches, and a speed regulating motor as a drive, and has a physical display function.
It has dynamic demonstrations of various working conditions of the ABS system and experimental functions, and a universal self-locking caster stand for easy mobile teaching.
II. Functions
1. The original vehicle circuit schematic diagram, oil circuit diagram, and external terminals are used to facilitate circuit detection and analysis; there is no need to pull out the electrical plug or puncture the wire, and practical teaching and practical training including resistance, voltage, and frequency can be carried out.
2. The pressure gauge displays the oil pressure of each cylinder when the ABS is working in real time, which is intuitive and clear.
3. The LED light meter simulates the real-time display of the working status of the sensor, solenoid valve, and hydraulic pump.
4. OBD-2 detection interface, which can be used to match, read data streams, fault code reading, system settings, matching, component execution, testing and other operations with detection instruments.
5. The panel uses a color ABS principle circuit diagram that is intuitive and easy to understand, durable and beautiful.
6. The overall stand is made of aluminum profiles, and the materials used, such as square tubes and angle steels, are made of national standard materials, and the surface is sprayed with plastic. Safe, reliable, durable, and mobile with universal casters.
III.ABS Principle
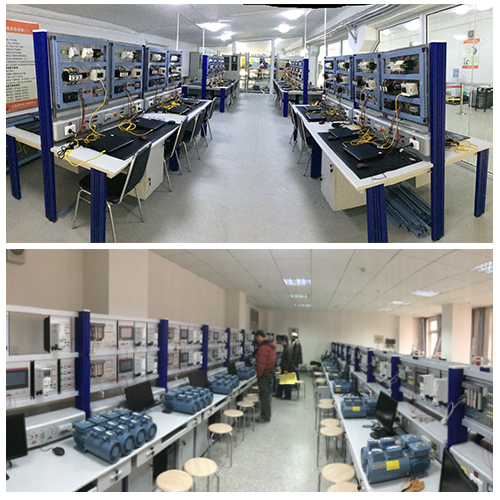
The full name of ABS is Anti-lock Brake System (anti-lock braking system) or Anti-skid Braking System (anti-skid braking system), which can effectively control the wheels to remain in a rotating state, improve the stability of the car during braking, and the braking performance of the car under poor road conditions. ABS continuously detects the speed of each wheel through the speed sensor installed on each wheel or drive shaft. The computer calculates the wheel slip rate at that time and compares it with the ideal slip rate to make a decision to increase or decrease the brake pressure, and command the actuator to adjust the brake pressure in time to keep the wheel in an ideal braking state.
In the common ABS system, a speed sensor is installed on each wheel to input the signal about the speed of each wheel into the electronic control device. The electronic control device monitors and determines the motion state of each wheel according to the signal input by each wheel speed sensor, and forms corresponding control instructions. The brake pressure regulating device is mainly composed of a pressure regulating solenoid valve, an electric pump and a reservoir, etc., forming an independent whole, which is connected to the brake master cylinder and each brake wheel cylinder through the brake pipeline. The brake pressure regulating device is controlled by the electronic control device to adjust the brake pressure of each brake wheel cylinder.
The working process of ABS can be divided into conventional braking, brake pressure maintenance, brake pressure reduction and brake pressure increase stages. In the normal braking stage, ABS does not intervene in the brake pressure control. All the inlet solenoid valves in the pressure regulating solenoid valve assembly are not powered and are in the open state, all the outlet solenoid valves are not powered and are in the closed state, and the electric pump is not powered to operate. The brake pipes from the brake master cylinder to each brake wheel cylinder are in the communication state, and the brake pipes from each brake wheel cylinder to the reservoir are in the closed state. The brake pressure of each brake wheel cylinder will change with the output pressure of the brake master cylinder. The braking process at this time is exactly the same as the braking process of the conventional braking system. During the braking process, when the electronic control device determines that a wheel tends to lock according to the wheel speed signal input by the wheel speed sensor, the ABS enters the anti-lock brake pressure adjustment process. For example, when the electronic control device determines that the right front wheel tends to lock, the electronic control device energizes the inlet solenoid valve that controls the scraping pressure of the right front wheel, and turns the right front fluid solenoid valve into a closed state. The brake fluid output by the brake master cylinder no longer enters the right front brake wheel cylinder. At this time, the right front outlet solenoid valve is still not energized and is in a closed state, and the brake fluid in the right front brake wheel cylinder does not flow out. The scraping pressure of the right front brake wheel cylinder remains constant, and the brake pressure of other wheels that do not tend to lock will still increase with the increase of the output pressure of the brake master cylinder. If the brake pressure of the right front brake wheel cylinder remains constant, the electronic control device determines that the right front wheel is still tending to lock, the electronic control device energizes the right front outlet solenoid valve and turns it into an open state, and part of the brake wave in the right front brake wheel cylinder will The fluid flows back to the reservoir through the open outlet solenoid valve, causing the brake pressure of the right front brake wheel cylinder to decrease rapidly, and the locking tendency of the right front wheel will begin to be eliminated. As the brake pressure of the right front brake wheel cylinder decreases, the right front wheel will gradually accelerate under the action of the vehicle's inertia force; when the electronic control device determines that the locking tendency of the right front wheel has been completely eliminated based on the signal input by the wheel speed sensor, the electronic control device cuts off the power to the right front fluid solenoid valve and the fluid outlet solenoid valve, turns the fluid inlet solenoid valve to the open state, and turns the fluid outlet solenoid valve to the closed state. At the same time, the electric pump is also energized to operate, and brake fluid is delivered to the brake wheel cylinder pump. The brake fluid output by the brake master cylinder enters the right front brake wheel cylinder through the solenoid valve, causing the brake pressure of the right front brake wheel cylinder to increase rapidly, and the right front wheel starts to lift and decelerate again.
The ABS structure diagram is as follows
ABS controls the slip rate of the wheel that tends to lock by cycling the brake pressure of the wheel that tends to lock, within the range of the peak adhesion coefficient slip rate, until the vehicle speed decreases to a very low level or the normal output pressure of the brake master cylinder no longer causes the wheel to lock. The frequency of the brake pressure regulation cycle can reach 3~20HZ. In this ABS, there is a pair of inlet and outlet solenoid valves corresponding to each brake wheel cylinder, which can be controlled separately by the electronic control device. Therefore, the brake pressure of each brake wheel cylinder can be adjusted independently, so that the four wheels will not be locked.
IV.Operation Instructions
1. Place the training system on a level hard ground and fix the self-locking casters of the system.
2. Check whether the components are loose during transportation. If they are loose, please handle them in time to avoid malfunctions during operation.
3. Check whether the matching connection lines of the training system are intact, whether there are any damages, and whether there are any water stains or dirt on the joints
4. Check whether the metal parts at the interface of the training system connection line are intact, and whether the pins are bent or disconnected.
5. Connect 220V and 380V AC power supplies, as shown below:
6. Turn on the "ignition switch" on the training system, the system is powered on, and the instrument lights up, indicating that the training system is powered on normally.
7. Press the motor start button, the power motor starts to drive the brake disc to rotate,
Brake disc
Hall signal sensor
8. Operate the speed control panel to adjust the speed according to your wishes.
9. When the speed regulator reaches the condition, press the brake pedal, and the analog indicator light on the panel flashes. ABS is connected to work.
Brake pedal
10. Press the motor stop button, the power motor stops and starts rotating.
11. Turn off the ignition switch, turn off the system power, and unplug the power plug. The experiment is over.
V. Fault Simulation System In Electrical System