MR119M Hybrid Electro Hydraulic And Electro Pneumatic Equipment Mechatronica Training Equipment Vocational Training Equipment
1. Equipment introduction
1.1 Overview
MR119M hybrid electro-hydraulic electro-pneumatic equipment adopts a double-sided structure, that is, one experimental bench provides students with a place for pneumatic and hydraulic experiments at the same time. It can conduct double-sided comprehensive pneumatic and hydraulic experiments at the same time, optimizing shared resources and improving product performance.
Through this set of practical training equipment, you can conduct pneumatic control and hydraulic control circuits and their corresponding basic application experiments. It can also be integrated with each other to conduct the following experiments: realize gas-electric control, gas-liquid control, electric-hydraulic control, and gas-electric-hydraulic integrated control.
1.2 Features
(1) This system can be used to design pneumatic and hydraulic circuits and learn pneumatic and hydraulic control technology.
(2) T-shaped slot aluminum platform enables quick connection of components.
2. Technical parameters
Total power input: three-phase AC220V
Size: 1550mm*860mm*1800mm
Weight: <282kg
Working conditions: Temperature -10℃~+40℃, relative humidity <85% (25℃)
3. Components list and detailed introduction
3.1 Hydraulic main part
No Name
1 Frame
2 Basic components (integrated tool box, hydraulic station, oil pan)
3 Universal wheel
4 Power supply hanging box
5 PLC hanging box
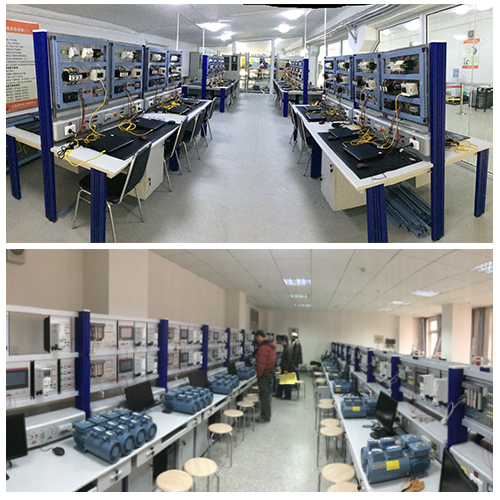
6 DC24 power supply hanging box
7 Emergency stop button hanging box
8 Button hanging box
9 Relay hanging box
10 Operation panel
3.2 Hydraulic components
No Name
1 Two-position four-way manual valve (transparent)
2 Three-position four-way manual valve (transparent)
3 Two-position four-way solenoid valve (single) (transparent)
4 Two-position four-way solenoid valve (double) (transparent)
5 Three-position four-way solenoid valve (double) (transparent)
6 One-way sequence valve (transparent)
7 One-way pressure reducing valve (transparent)
8 Pilot-operated check valve (transparent)
9 One-way throttle valve (transparent)
10 Throttle valve with pressure compensation (transparent)
11 Bidirectional hydraulic motor (transparent)
12 Double-acting cylinder with stroke collision block (transparent)
13 Pressure gauge (transparent)
14 Three-way valve (transparent)
15 Hydraulic auxiliary oil tank (transparent)
16 Hydraulic hose
3.3 Pneumatic main part
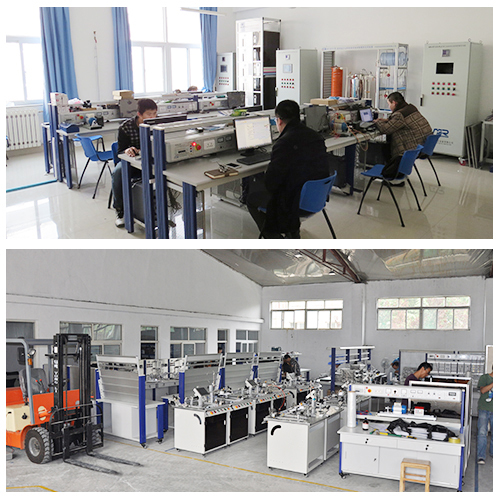
No Name
1 Frame
2 Basic components (integrated tool box, air pump, oil pan)
3 Universal wheel
4 Operation panel
5 Power supply hanging box
6 DC24 power supply hanging box
7 PLC hanging box
8 Relay hanging box
9 Time relay hanging box
10 Button hanging box
11 Emergency stop button hanging box
12 Buzzer hanging box (not marked in the picture)
3.4 Pneumatic components
No Name
1 Three-position five-way manual valve
2 Two-position three-way solenoid valve
3 Two-position five-way solenoid valve
4 Three-position five-way solenoid valve
5 delay valve
6 Knob button valve
7 Quick exhaust valve
8 Two-position three-way stroke valve
9 Micro Switch
10 Limit switch
11 Single port three-position valve
12 Pneumatic travel switch mechanical valve
13 One-way throttle valve
14 doublet
15 Double pressure valve
16 Pneumatic multi-pipe exhaust
17 capacitive sensor
18 Inductive sensor
19 Photoelectric Sensors
20 trachea
21 single acting cylinder
22 Double acting cylinder
23 Flat head button type three-position valve
24 Pressure transmitter with digital display
3.5 Introduction to hydraulic components
3.6 Introduction to pneumatic components
3.7 Accessories
No Name Qty
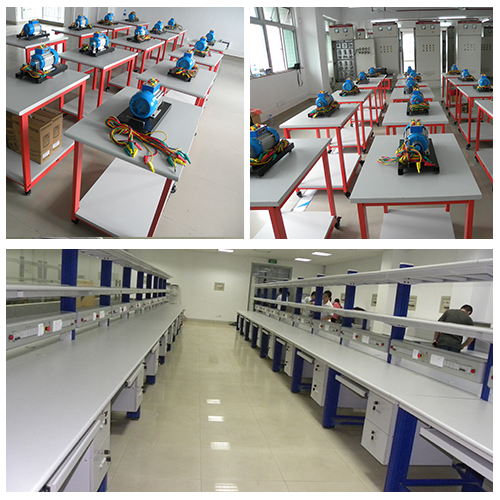
1 2mm safety connection cable (red) 20
2 2mm safety connection cable (blue) 20
3 2mm safety connection cable (black) 20
4 2mm safety connection cable (yellow) 20
5 2mm safety connection cable (green) 20
6 Insurance tube (3A) 5
7 Insurance tube (10A) 5
8 raw tape 1
9 4mm safety connection cable (yellow) 1
10 4mm safety connection cable (blue) 1
11 European plug 1
12 European power cord 2
4. Experiment list
Experiment 1 Hydraulic Station Introduction Experiment
Experiment 2 Two-position four-way manual valve operation experiment
Experiment 3 Three-position four-way manual valve operation experiment
Experiment 4 Two-position four-way solenoid valve operation experiment
Experiment 5 Three-position four-way solenoid valve operation experiment
Experiment 6 One-way pressure reducing valve operation experiment
Experiment 7 Pilot check valve (hydraulic control one-way valve) operation experiment
Experiment 8 Research on the relationship between throttle valve opening and closing and pressure difference
Experiment 9 Hydraulic motor operation experiment
Experiment 10 Delay valve operation experiment
Experiment 11 Flat head button type three-position valve operation experiment
Experiment 12 Knob button valve operation experiment
Experiment 13 Micro switch operation experiment
Experiment 14 Three-position five-way solenoid valve operation experiment